Monorail-Hanger type shot blasting machine for Foundry
The Monorail Hanger Type Shot Blasting Machine is a versatile and efficient surface treatment equipment designed for foundry applications. It is particularly suitable for cleaning, deburring, and surface preparation of castings, forgings, and other workpieces. The machine operates by blasting abrasive materials (typically steel shots or grits) onto the workpieces, effectively removing surface contaminants, such as sand, rust, and scale.
The pass-through Hanger Type Shot Blasting Machine offers numerous advantages, such as high productivity, consistent results, and reduced labor costs. It is an ideal solution for foundries and other industries that require efficient surface treatment of large or complex workpieces.
The category of the foundry:
The foundry industry is generally classified as a part of the manufacturing sector.
Specifically, it is a subcategory of the metal casting industry, which involves the production of metal components by pouring molten metal into a mold and allowing it to solidify.
Foundries typically specialize in casting specific types of metal, such as iron, steel, aluminum, copper, or brass. The products produced by foundries include a wide variety of metal parts and components, ranging from small and simple to large and complex, which are used in various industries such as automotive, aerospace, construction, and more.
Key benefits of using a monorail-hanger type shot blasting machine for the foundry:
Monorail hanger type shot blasting machines, AKA pass-through hook type shot blasting machines, are highly efficient in removing contaminants such as sand, scale, and rust from castings. The machine’s high-speed blast wheel throws steel shots onto the surface of the casting, which removes the contaminants and leaves a clean surface.
The monorail hanger type shot blasting machine ensures consistent quality of the cleaned castings. The machine is designed to provide uniform blast coverage on every part of the casting, which ensures that all the contaminants are removed, and the surface is evenly cleaned.
Using a monorail hanger type shot blasting machine reduces the need for manual labor in the cleaning process. The machine is designed to handle large volumes of castings, and it can clean multiple castings simultaneously, which reduces the need for manual labor and saves time and money.
The shot blasting process removes contaminants from the surface of the casting, which helps prevent corrosion and extends the life of the castings and the machine itself. By using a monorail hanger type shot blasting machine, the life of the equipment is prolonged, and maintenance costs are lowered.
The pass-through hanger type shot blasting machine is designed to be environmentally friendly. The machine uses steel shots as the blasting media, which can be recycled and reused, reducing waste in the process. Additionally, the machine’s dust collection system captures the dust generated during the shot blasting process, improving air quality in the foundry.
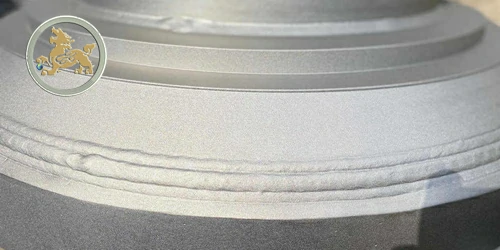
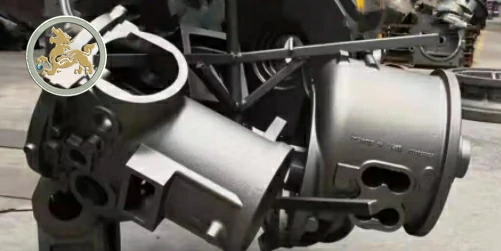
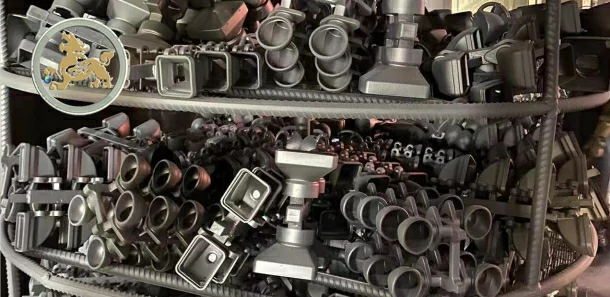
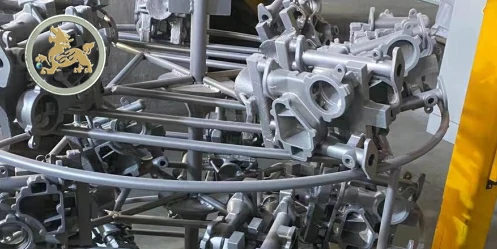
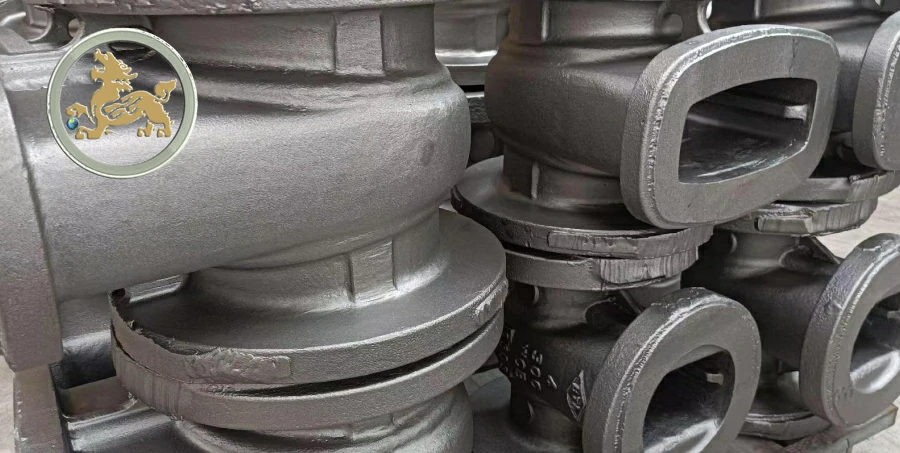
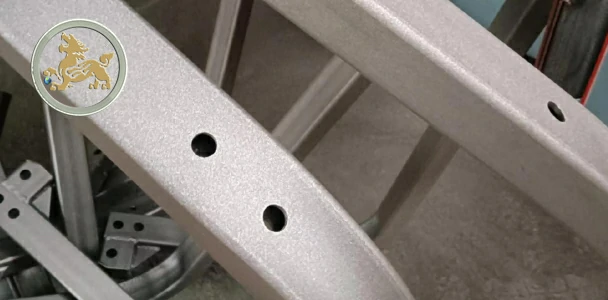
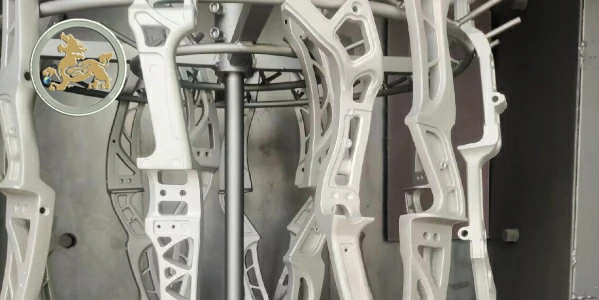
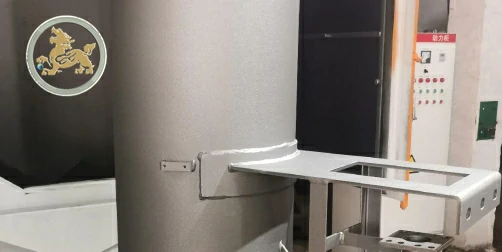
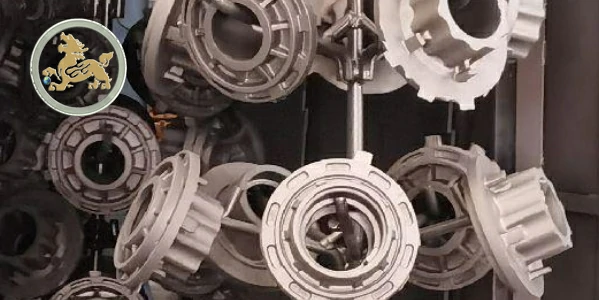
FAQ of hanger type shot blasting machine for the foundry:
A shot blasting machine is a piece of equipment used for cleaning, preparing, and/or finishing the surface of a material by propelling abrasive particles (or “shots”) onto its surface at high velocity. The machine is designed to remove contaminants such as rust, scale, paint, and other surface impurities, leaving a clean and textured surface.
The shot blasting process involves using a turbine or blast wheel to propel the abrasive particles onto the surface of the material. The abrasive particles can be made of materials such as steel shot, grit, sand, or other types of abrasive media. The type of abrasive media used depends on the specific application and the type of surface being processed.
Shot blasting machines are used in various industries, such as automotive, aerospace, construction, foundries, and shipbuilding. They can be used for surface preparation, cleaning, and finishing of a wide range of materials, including metal, concrete, brick, and stone.
There are several types of shot blasting machines, including tumble blast machines, table blast machines, hanger-type blast machines, and continuous blast machines. Each type of machine has its own unique features and advantages, and the choice of machine depends on the specific requirements of the application.
Refer to this guideline chart of the wheelabrator buying a shot blasting machine. Check it and compare it with your sourcing budget, but please bear in mind that the cost of the shot blasting machine is just for your information, the different purpose and workload needs the shot blasting machine’s shot wheels, motor, quantity, brand, automated level all different, so the final cost please contact us for confirm;
Main Components of a Monorail Hanger Type Shot Blasting Machine:
Shot Blast Cabinet: The blast cabinet is the primary enclosure where the workpieces are hung and the shot blasting process takes place. It is designed to be robust and wear-resistant, often lined with wear-resistant materials like manganese steel or rubber.
Monorail System: This system consists of a motorized overhead conveyor that transports the workpieces through the blast cabinet. The monorail system allows for continuous or batch processing, depending on the production requirements.
Hangers: The hangers are designed to hold the workpieces securely during the blasting process. They can be manually or automatically loaded and unloaded, depending on the size and weight of the workpieces.
Blasting Wheel: The blasting wheel is the main component responsible for propelling the abrasive materials at high velocity towards the workpieces. It is powered by an electric motor and typically has multiple vanes or impellers for optimal abrasive distribution.
Abrasive Recovery System: This system recovers and recirculates the used abrasive materials for continuous operation. It typically consists of a screw conveyor, bucket elevator, and air separator, which separate the reusable abrasive from the waste material.
Dust Collection System: A dust collector is essential for maintaining a clean working environment and complying with environmental regulations. It removes dust and other fine particles generated during the blasting process through a system of filters or cyclones.
Control System: The control system manages the operation of the machine, ensuring optimal performance and efficiency. It typically includes PLC (Programmable Logic Controller) controls and HMI (Human-Machine Interface) for easy operation and monitoring.
Here are five key benefits of using a shot blasting turbine:
- Efficient surface preparation: Shot blasting turbines are highly efficient in removing surface contaminants and preparing surfaces for subsequent processing operations. They are capable of removing rust, scale, paint, and other impurities from a variety of surfaces, including metal, concrete, and stone.
- Consistent results: Shot blasting turbines provide consistent results, ensuring that surfaces are thoroughly cleaned and prepared to the desired level of finish. This helps to ensure that subsequent coatings and finishes adhere properly and last longer.
- Versatile: Shot blasting turbines can be used for a wide range of applications, including surface preparation, cleaning, and deburring. They can be used on a variety of surfaces and materials, making them a versatile tool for many industries.
- Environmentally friendly: Shot blasting turbines can be used with a variety of blasting media, including steel shot, glass beads, and plastic media. This allows for the use of environmentally friendly blasting media, reducing the impact of the blasting process on the environment.
- Cost-effective: Shot blasting turbines are a cost-effective solution for surface preparation and cleaning, offering a high return on investment due to their efficiency and durability. They can be used in a variety of applications, reducing the need for multiple machines and equipment, further reducing costs.
The shot blasting machine market for foundry is a growing industry, driven by increasing demand for high-quality castings with improved surface finish, durability, and strength. Shot blasting machines are used in foundries for cleaning, descaling, and surface preparation of castings before further processing such as painting or coating.