Carousel-Hanger type shot blasting machine for Foundry
The carousel hanger type shot blasting machine for foundry is an advanced surface treatment equipment designed for cleaning, descaling, and surface preparation of castings, forgings, and other workpieces in foundry environments. This machine features a rotating carousel mechanism with multiple hangers, on which the workpieces are hung and then exposed to high-velocity abrasive blast media.
The carousel hook type shot blasting machine for foundry is a highly efficient and versatile surface treatment solution for various foundry applications, providing consistent and uniform cleaning, descaling, and surface preparation.
The category of the foundry:
Ferrous foundries specialize in casting iron and steel alloys;
Non-ferrous foundries specialize in casting non-ferrous metals such as aluminum, copper, brass, bronze, and zinc.
Within each of these categories, foundries can further specialize in specific types of casting processes, such as sand casting, investment casting, die casting, or continuous casting.
Key benefits of using carousel-hanger type shot blasting machine for the foundry:
The rotating carousel mechanism ensures that all workpieces receive consistent and uniform treatment, resulting in improved productivity.
It can accommodate a wide range of workpiece sizes and shapes, making it suitable for various foundry applications.
The automated nature of the shot blasting machine reduces the need for manual handling and labor-intensive operations.
The shot blasting machine produces a uniform, clean surface on the workpieces, improving their overall quality and appearance.
The closed-loop abrasive media recovery system and dust collection system minimize waste generation and environmental impact.
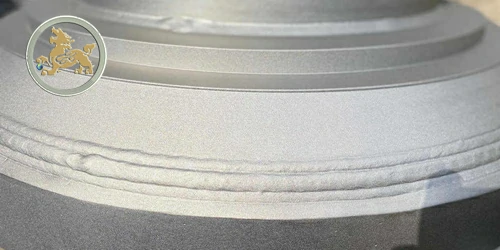
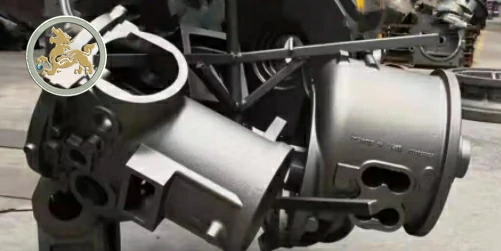
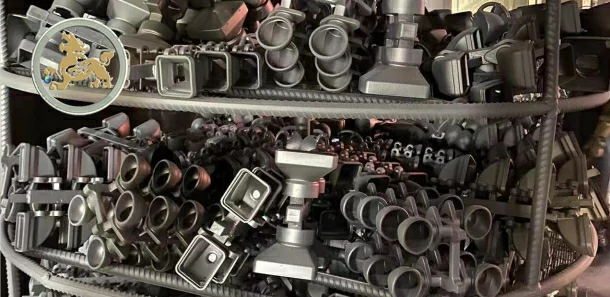
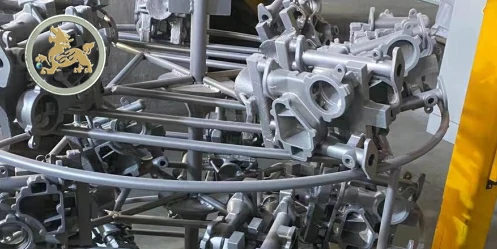
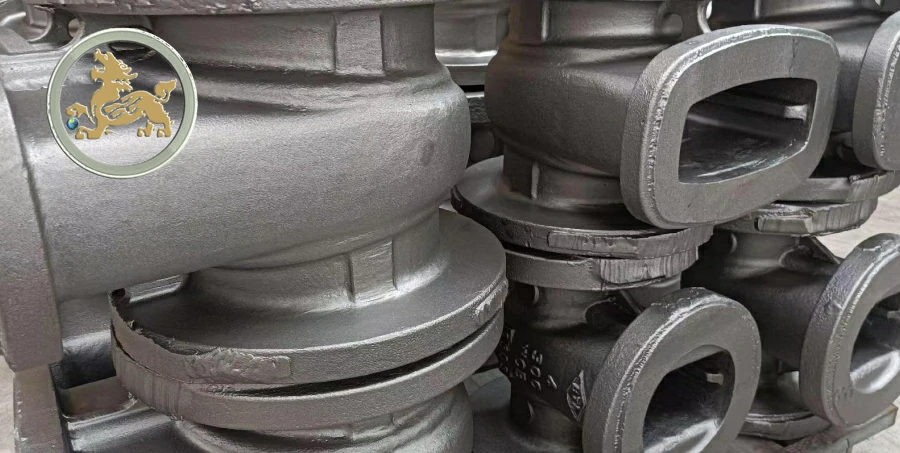
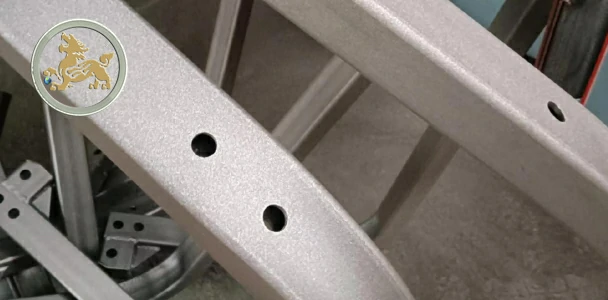
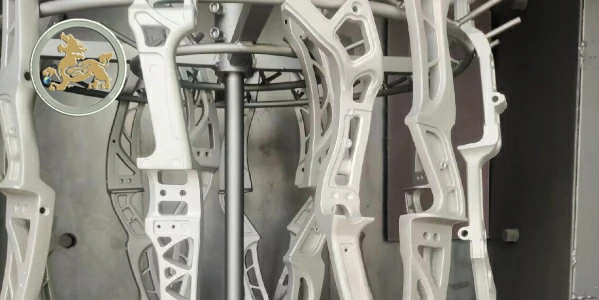
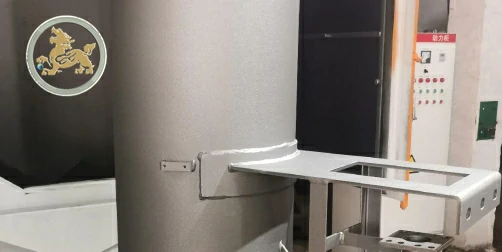
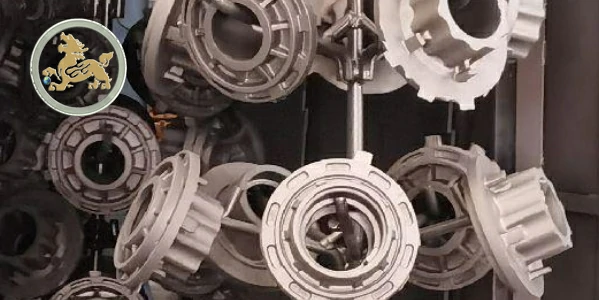
FAQ of hanger type shot blasting machine for the foundry:
A shot blasting machine is a piece of equipment used for cleaning, preparing, and/or finishing the surface of a material by propelling abrasive particles (or “shots”) onto its surface at high velocity. The machine is designed to remove contaminants such as rust, scale, paint, and other surface impurities, leaving a clean and textured surface.
The shot blasting process involves using a turbine or blast wheel to propel the abrasive particles onto the surface of the material. The abrasive particles can be made of materials such as steel shot, grit, sand, or other types of abrasive media. The type of abrasive media used depends on the specific application and the type of surface being processed.
Shot blasting machines are used in various industries, such as automotive, aerospace, construction, foundries, and shipbuilding. They can be used for surface preparation, cleaning, and finishing of a wide range of materials, including metal, concrete, brick, and stone.
There are several types of shot blasting machines, including tumble blast machines, table blast machines, hanger-type blast machines, and continuous blast machines. Each type of machine has its own unique features and advantages, and the choice of machine depends on the specific requirements of the application.
Refer to this guideline chart of the wheelabrator buying a shot blasting machine. Check it and compare it with your sourcing budget, but please bear in mind that the cost of the shot blasting machine is just for your information, the different purpose and workload needs the shot blasting machine’s shot wheels, motor, quantity, brand, automated level all different, so the final cost please contact us for confirm;
Main Components of a Carousel Hanger Type Shot Blasting Machine:
- Carousel Mechanism: The carousel hanger system consists of a rotating platform that holds multiple hangers or hooks. Workpieces are suspended from these hangers, and as the carousel rotates, each workpiece passes through the blast chamber, ensuring uniform cleaning and surface preparation.
- Blast Chamber: The blast chamber is the main area where the workpieces are exposed to the abrasive blast media. It is lined with wear-resistant materials to withstand the high-velocity impact of the blast media.
- Blast Wheel(s): One or more high-power centrifugal blast wheels are used to propel the abrasive media at high speeds towards the workpieces. The blast wheels are strategically positioned to ensure efficient and uniform cleaning of the workpieces.
- Abrasive Media Recovery System: A media recovery system is in place to collect, clean, and recycle the abrasive media for continuous operation. This system usually consists of a screw conveyor, bucket elevator, air separator, and media storage hopper.
- Dust Collection System: A dust collection system is used to remove dust and fines generated during the blasting process, maintaining a clean and safe working environment. This system typically includes a baghouse filter or cartridge filter, a fan, and ductwork.
Here are five key benefits of using a shot blasting turbine:
- Efficient surface preparation: Shot blasting turbines are highly efficient in removing surface contaminants and preparing surfaces for subsequent processing operations. They are capable of removing rust, scale, paint, and other impurities from a variety of surfaces, including metal, concrete, and stone.
- Consistent results: Shot blasting turbines provide consistent results, ensuring that surfaces are thoroughly cleaned and prepared to the desired level of finish. This helps to ensure that subsequent coatings and finishes adhere properly and last longer.
- Versatile: Shot blasting turbines can be used for a wide range of applications, including surface preparation, cleaning, and deburring. They can be used on a variety of surfaces and materials, making them a versatile tool for many industries.
- Environmentally friendly: Shot blasting turbines can be used with a variety of blasting media, including steel shot, glass beads, and plastic media. This allows for the use of environmentally friendly blasting media, reducing the impact of the blasting process on the environment.
- Cost-effective: Shot blasting turbines are a cost-effective solution for surface preparation and cleaning, offering a high return on investment due to their efficiency and durability. They can be used in a variety of applications, reducing the need for multiple machines and equipment, further reducing costs.
The shot blasting machine market for foundry is a growing industry, driven by increasing demand for high-quality castings with improved surface finish, durability, and strength. Shot blasting machines are used in foundries for cleaning, descaling, and surface preparation of castings before further processing such as painting or coating.
- Steel shot and grit are the most commonly used abrasives for shot blasting in foundries. They are made from hardened steel and are highly durable, making them effective for removing surface contaminants and creating a uniform surface finish on metal parts.
- Aluminum oxide is another popular abrasive material that is commonly used for shot blasting. It is a sharp and durable abrasive that is effective for removing rust, scale, and other surface contaminants. It is also used for surface preparation prior to coating or painting.
- Garnet and glass beads are also used as abrasives for shot blasting. Garnet is a natural mineral that is highly durable and effective for removing surface contaminants without damaging the underlying metal. Glass beads are made from recycled glass and are gentle enough for use on delicate surfaces.