Installation Conditions & Guidelines for Shot Blasting Machines
A shot blasting machine install requires careful consideration of several necessary conditions. These conditions ensure the proper functioning, safety, and longevity of the equipment. Here are some key factors to consider:
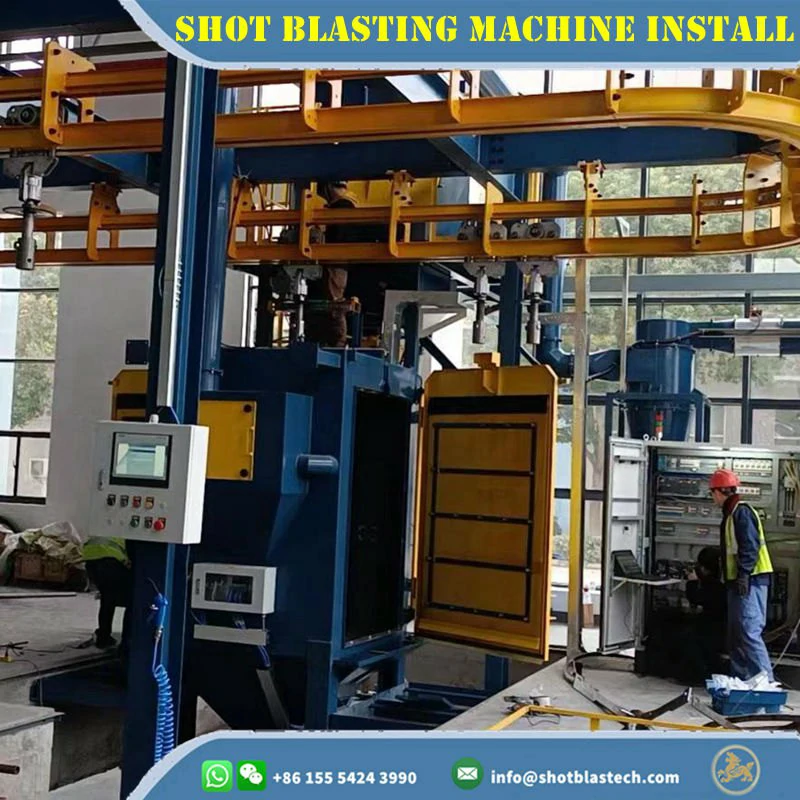
- Foundation: The shot blasting machine requires a solid and accurately sized foundation to support its weight, withstand vibrations, and prevent movement. A sturdy foundation minimizes vibrations by securely fixing the machine to the foundation.
- Space: Allocate sufficient space for the shot blasting machine, considering its dimensions, and allowing for maintenance, loading, and unloading operations. Ensure an ample gap between the control panel and blast wheel assembly for safety.
- Workshop Environment: Install the shot blasting equipment in a dedicated workshop that is dry and protected from rain. This safeguards electrical components and prevents abrasive media from rusting. If a dust collector is present, it can be placed outdoors with a rain-proof shed unless specified otherwise. Construct a simple workshop structure if necessary to protect the equipment and optimize serviceability.
- Avoidance of Running Water: Install the shot blasting machine away from areas prone to running water to avoid operational issues, electrical damage, and safety risks.
- Elevator Tensioning: Properly tension the elevator’s belt during installation. The drive chain should exhibit a sagging degree of 2% to 4% of the center distance between the chain wheels to ensure optimal functionality and performance of the elevator system.
- Maintenance and Transportation Accessibility: Consideration should be given to the accessibility of the equipment for maintenance and transportation purposes. The installation location should allow convenient access to all components that require regular inspection, servicing, or replacement. Furthermore, the impact on the surrounding environment, such as noise levels or emission control, should also be taken into account.
- Power Supply: Sufficient and stable power supply should be available at the installation site to meet the equipment’s electrical requirements. It is essential to ensure that the power source matches the machine’s specifications and that appropriate electrical connections are in place.
- Ventilation: Adequate ventilation should be provided in the installation area to remove dust, fumes, and exhaust generated during the shot blasting process. Proper ventilation helps maintain a safe and healthy working environment for operators and prevents the accumulation of airborne contaminants.
- Lighting: Satisfactory lighting conditions should be established in the installation area to ensure proper visibility during operation, maintenance, and inspection of the shot blasting machine. Sufficient illumination enhances safety and productivity.
- Floor Condition: The condition of the floor where the shot blasting machine will be installed is crucial. It should be flat, level, and capable of supporting the equipment’s weight. Any irregularities or weaknesses in the floor should be addressed to prevent operational issues or structural damage.
- Accessibility: The installation site should allow for easy access to the shot blasting machine from all sides. Sufficient space should be provided for operators to maneuver around the equipment safely and efficiently. This facilitates maintenance tasks, equipment adjustments, and troubleshooting.
- Noise Control: Measures should be taken to mitigate noise levels generated by the shot blasting machine. Soundproofing or noise-reducing materials can be installed to minimize noise pollution and protect the hearing health of operators and nearby personnel.
- Safety Measures: Adequate safety measures, such as emergency stop buttons, safety interlocks, and protective barriers, should be implemented to ensure operator safety during equipment operation. Safety protocols and training should also be provided to personnel working with or near the machine.
- Environmental Considerations: Environmental impact assessments should be conducted to address any potential environmental concerns associated with the shot blasting machine’s installation and operation. Appropriate measures, such as dust collection systems or emission controls, should be implemented to minimize pollution and comply with relevant regulations.
- Utilities and Services: Necessary utilities and services, such as compressed air supply, water supply (if required), and drainage systems, should be available and properly connected to the shot blasting machine. These utilities are often essential for the equipment’s optimal performance and functionality.
- Documentation and Compliance: All relevant documentation, including manuals, specifications, and safety certifications, should be obtained and reviewed. It is essential to comply with local regulations, industry standards, and any specific requirements outlined by the manufacturer or project specifications.
By meeting these essential conditions, the installation of the shot blasting machine can be optimized for enhanced performance, durability, and functionality. Addressing these additional requirements ensures effective installation, promoting operational efficiency, safety, and compliance with relevant standards.