Exploring the Depths of Barrel Shot Blasting Machine
The blasting chamber of the barrel shot blast machine is constructed using wear-resistant alloy steel and equipped with durable annular rubber belts, ensuring exceptional strength and rigidity. The layout of the shot blasting turbine is meticulously designed using advanced 3D dynamic simulation, guaranteeing optimal blasting angles and distances. Within the hot zone, aka the direct-blasting area, high-manganese steel lining with a remarkable hardness of up to 60HRC is employed, which can be easily replaced when necessary.
During operation, the processed parts are placed into the shot blasting chamber, either manually or in automatic mode. As the drum rotates, the parts undergo continuous rolling, ensuring a comprehensive 360° coverage of the surface. The result is a flawlessly cleaned workpiece, devoid of oil stains, oxide scale, rust, paint coatings, or any other undesired attachments.
The placement position and design of the shot turbine are specially tailored to accommodate workpieces from various angles within the drum, effectively reducing blasting time and realizing the principles of high efficiency and cost-effectiveness. This barrel shot blasting machine boasts several notable features, including a large shot blasting volume, fast injection speed, low noise levels, wide-angle coverage, and superior cleaning efficiency. The specialized distributor structure ensures a high rate of shot blasting. Additionally, the machine is designed for easy maintenance, minimizing downtime.
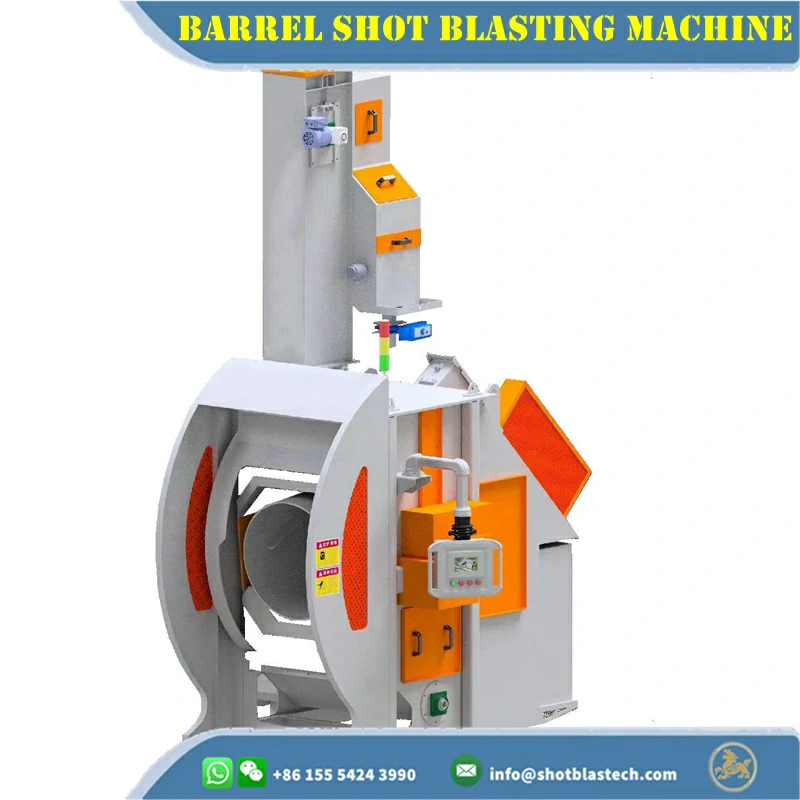
The barrel shot blast machine serves several important functions:
By utilizing a high-speed rotating impeller to propel steel shots onto the constantly rotating workpieces within the drum, it achieves the goal of thoroughly cleaning the workpieces. It finds applications in various industries, such as sand removal, rust removal, scale removal, and surface strengthening of forgings. It effectively eliminates burrs, paint, rust, and other contaminants that may compromise the integrity, appearance, or clarity of the objects. Furthermore, it can remove surface impurities from coated surfaces and enhance the contours of additive coatings, thereby improving the workpieces. The machine is particularly well-suited for cleaning a wide range of castings and forgings that can withstand collisions and scratches. In small heat treatment workshops, the Cyclone Blast serves as an ideal tool for removing residual sand and scale from workpiece surfaces. It is also a preferred choice for cleaning parts that frequently get caught or stuck in traditional crawler shot blasting machines, thus minimizing the risk of damage to the parts.
The drum-type shot blasting machine incorporates several additional features and functionalities:
- The shot blasting chamber is lined with a 25 mm thick layer of robust manganese steel, ensuring exceptional durability and resistance to wear. The welding process employed in constructing the barrel eliminates any dead spots and sharp edges that could potentially scratch or damage the workpieces, guaranteeing their integrity and safety.
To accommodate different shapes and types of parts, the machine is equipped with a replaceable actuator cone. This cone can be easily swapped out to provide optimal peening performance for various workpiece configurations, allowing for versatile and efficient operation.
For improved operational efficiency and safety, the machine is equipped with a press-button door sealing device.
The machine offers full automation capabilities, allowing for higher productivity and increased throughput. With automated processes, such as part loading, shot blasting, and unloading, the machine significantly reduces manual intervention, streamlines operations, and optimizes overall production efficiency.
The use of wear-resistant (WR) screws further enhances the machine’s longevity and performance. These specially designed screws exhibit exceptional resistance to wear and tear, ensuring reliable and efficient operation over an extended period.
The machine incorporates a multi-point support cylinder, providing enhanced stability and durability during the rotation of the drum. This design feature contributes to smooth and consistent operation, minimizing vibrations and maximizing the machine’s lifespan.
The drum angle of the machine is adjustable, facilitating the loading and unloading process. This adjustable feature, combined with impact load suspension, ensures convenient access to the shot blasting chamber, simplifying the handling of workpieces and enhancing overall operational efficiency.
This device ensures a secure and airtight seal when the shot blasting chamber is closed, eliminating any potential air leakage or loss of pressure. The press-button mechanism guarantees a reliable seal, maintaining the machine’s performance while minimizing the possibility of dust or abrasive particles escaping during operation.
These additional features enhance the functionality, versatility, and convenience of the barrel-tilted shot blasting machine, making it a reliable and efficient solution for various surface preparation and cleaning applications.