Advantages of Shot Blasting for Surface Preparation
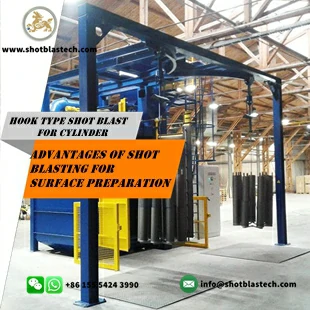
Shot blasting has various advantage with one of the most effective, possibly the cheapest technique and become of vital process for metal surface finishing preparation prior to operations such as galvanizing, electroplating, welding, enameling, glass coating, painting and rubberizing, etc.
Shot blasting is useful for many ferrous and non-ferrous industries, including the foundry, aerospace, ship building, forging and metal industries because it provides a consistent and uniformly fine, rough or matt surface depending on the surface requirement and following process such as: cutting, drilling, welding processes, etc.
The major benefits of shot blasting as a surface preparation technicle:
- Shot blasting eliminates the dust-emission on site and output of dust collector;
- Shot blasting provides higher production rates but with lower cost, wider recycle abrasive selection;
- Shot blasting with optimal shot-wheel-turbine projectile angle and capacity, to achieve of best blast pattern accuracy and enhanced finish consistency, universal roughness standard; It also helps to expose of metal surface faults or defects beneath;
- The finished surface obtained is absolutely environmental-safety such as free from chemical deposits and dust pollution;
- Shot blasting’s projectile angle and capacity does not remove any virgin metal when removing scales, rust and surface dust;
- Shot blasting’s surface cleaning is guarantee of between of the metal and the protective coat (zinc, paint or epoxy). It can greatly improve of lifespan and durability of protective surface coats as it adheres better to the shot blast cleaned and scale free surface.
There are many other reasons for the benefit of labor-cost saving with automatic operation, the shot blasting can work with the following process of painting, coating etc.
Types of Shot-abrasive Used:
While shot blasting primarily refers to blasting the surface with small steel pellets (balls) or shots grit, many other types and material of shot blast materials are also used.
- Steel Shots– Steel balls of diameter 0.5 to 2.0 mm are fired at high speed (70m/s to 90m/s) against the surface being prepared. The material and size of the shot-steel determines the finishing standard (common use of Sa 21/2). Smaller steel-shots are used for fine polished surface, while larger diameter lead to a rougher finish.
- Steel Grit– Shot lasting with steel grit (irregular shape) is used for surface where aggressive cleaning is required, such as for removing very adhesive contaminants (concrete, resin or epoxy) from metal surface.
- Aluminum Grit– The aluminum material specially use for the aluminum surface, the surface like the car wheel made of aluminum; but during of using you should take caution of the exposive.
- There are many other materials of shot media used, such as the glass bead etc. which is one-time use for the sand blasting.