Shot wheel turbines
Low cost, easy maintenance, high efficiency, wear resistance, compact structure and energy saving.
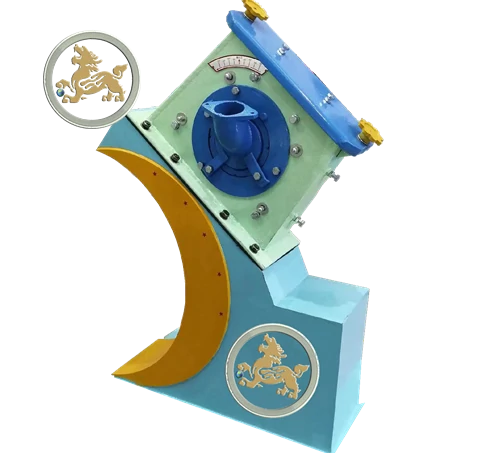
The shot blasting wheel turbines assembly is essential to the shot blasting machine. The quality of the shot blasting turbines directly affects the results of the shot blasting. It is usually the largest propositional consumables and one of the most maintenance-intensive components of the shot blasting machine. The overall life span is also the largest factor in production costs, which is vital to profitability. If properly maintained, the life of the turbine shot blasting machine can be significantly extended, thereby reducing the cost of use.
The performance of the shot blasting device depends on the quality, quantity, speed and direction angle of the shot-projectile; the last three factors depend entirely on the selection, design, installation and correct operation of the shot blasting equipment.
Feature of the wheelabrator shot turbines:
- Compact shell structure, longer lifespan of blades, lower maintenance;
- Upgraded wearing-resistance with low working noise & vibration;
- High-speed blasting capacity with more recycle abrasive using;
- Optimal blasting angle, velocity and energy-saving;
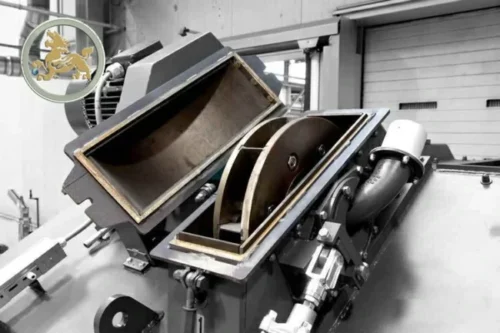
The main type of the wheelabrator shot turbines:
Direct-drive shot blasting turbine is a compact structure in the shot blasting machine. The motor and the shot turbine are directly connected by a shaft. So its structure is more compact, more efficient, quieter and easy to maintain.
Normally the maximum motor power is 15kW, and the maximum blasting capacity is 250 kg/min.
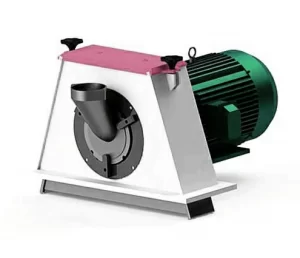
Belt-driven shot blasting turbine is the most popular in the shot blasting machine. The motors and the shot wheel turbine is connected by a belt. More blasting flow and higher power can be obtained, and the cleaning effect is stable, the capacity is 15-75kw, the maximum blasting volume is 950kg/min.
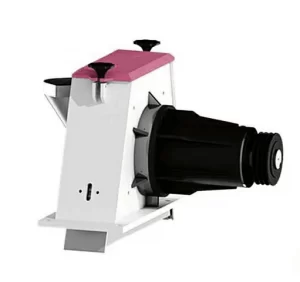
The spare parts we manufacture for automatic shot blasting turbines include:
- Blades (8pcs per set) with balanced quality: wear-resistant castings, tool steel and tungsten carbide.
- Impeller, distributor, accelerator, projector.
- Deflector, feed valve, cover, shell.
- Lining, wear liner, protective plate, cover, shell: top, side, end…
- Rotor, wheel, disc or impeller.
- Feeding or supply chute, steel shot projector.
- Clips, wheels.
- Centering board.
- Screw, spring, blade clamping element.
- Wheel cover: body, side, cover, clip.
- More information…
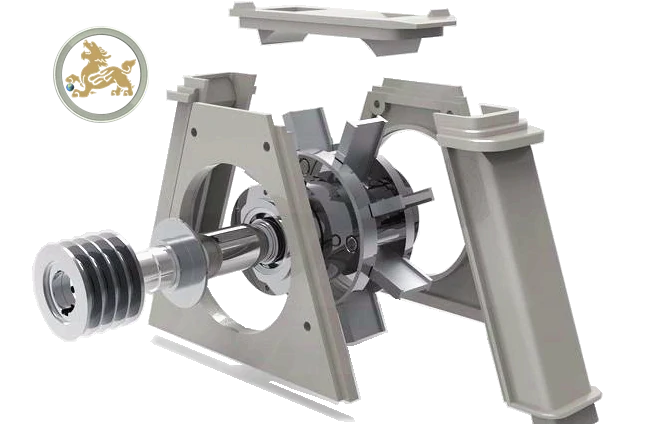
Working Principle of Shot Blast Wheel Turbine Assembly:
- Steel shots or shot grit goes into the impeller from the abrasive feed chute. Impeller and blades continuously self-rotate at very high speed (more than 75m/s) driven by a motor (Direct-connect or Belt connect to the shot turbines). Steel shots through the impeller and deflector out and relay by rotating blade. Blades push shot steels with high speed out from the opening at the bottom of the shot wheel turbine shell. To make the shot blasting in good condition, impeller, deflector and blades should be correctly adjusted angle and certain projectile speed, and the shot abrasive flows should impact mostly of the workpieces and the 1st impact area focus on the protective plates.
- Abrasive Circulation System: The disk of the shot blast wheel assembly unit projector is abrasive and finally down by gravity and gather into a hopper located at the bottom of the shot blasting room; Through the screw conveyor, the shot steel transfers to the boot of the bucket elevator. These shot abrasives are lifted to the desired height with the help of buckets mounted on wearing-resistance rubber belts. The tensioning arrangement device for the elevator belt is provided at the bottom portion of the elevator which is easier to maintain, make sure no spillage of the belt.
- Abrasive purify System: Oversize contaminants and the abrasive mixture is discharged from the top section of the bucket elevator into the magnetic separator by means of an upper screw conveyor. After of 3-class of magnetic separating, the abrasive mixture will be classified: trashes will be directed discharge into a trash drum; the fine dust particles will be conveyed through vent piping to the dust collector; the useful shot steels will drop into a reuse hopper and thereafter to the abrasive feed valve controlled by pneumatic electromagnetic valves.
Best Shot Blasting Machine Manufacturer:
Sino wheelAbrator professionals design, support, manufacture and service shot blasting and surface preparation machines and related shot blasting products for a wide range of industries, cleaning, derusting, descaling and surface hardening. Improvements can be made by upgrading to newer technology.
We offer world-class shot blasting and sandblasting machines along with new innovative ideas and concepts to eliminate old design problems with shot blasting equipment.